Using Technology to Overcome Natural Disasters in Logistics
Recent “once in a lifetime” flooding left supplies in WA stranded. How can logistics tech enable shippers and carriers to react more efficiently to natural disasters?
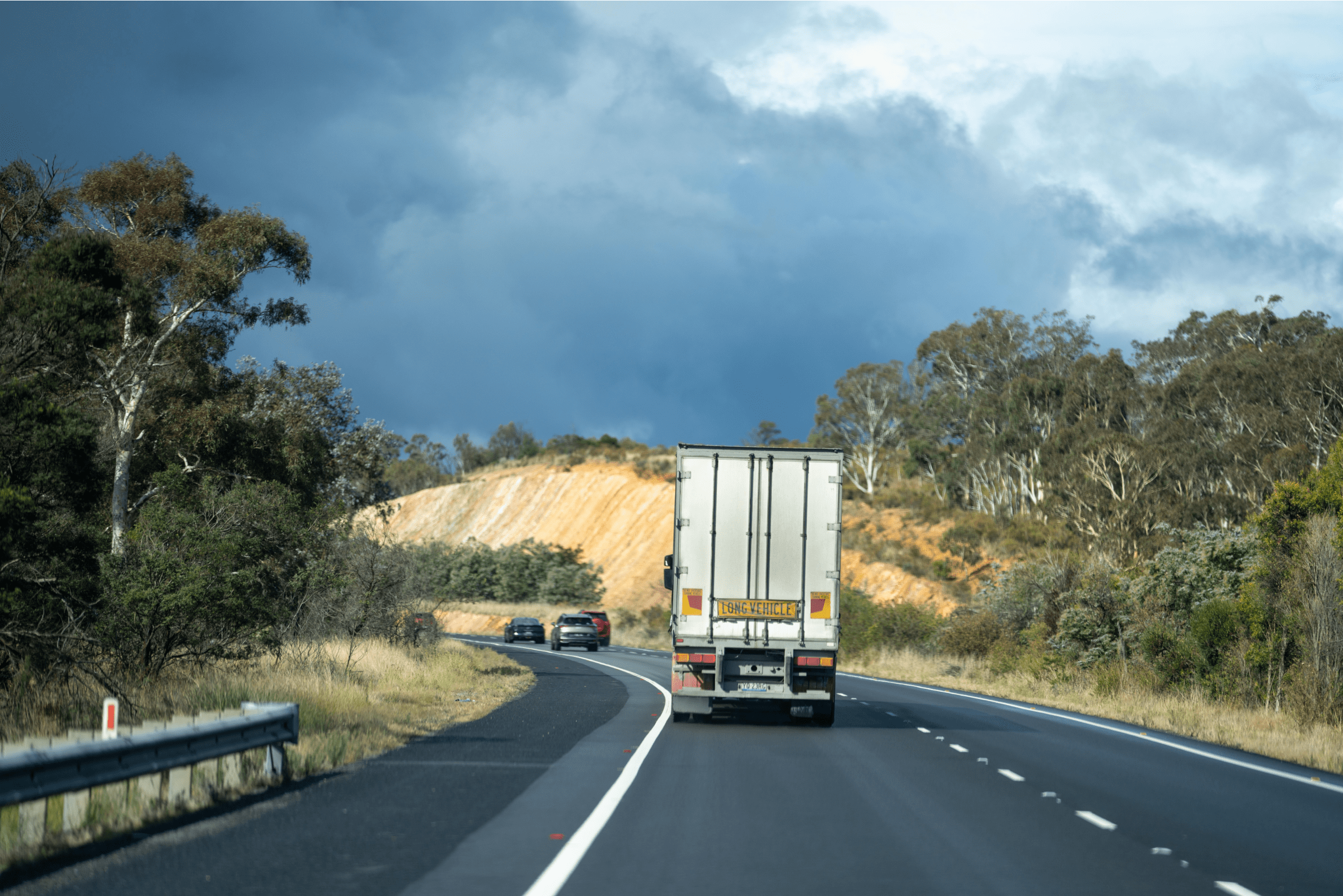
In the last few years, the logistics industry has been increasingly tested by the unpredictability of natural disasters. A recent example of this challenge unfolded in Western Australia, where unprecedented rainfall disrupted the essential flow of goods. This created a serious problem for supply chains across the region.
In the past,logistics companies were forced to handle these situations through time-consuming manual processes, relying on phone calls, faxes, emails and physical paperwork in order to reroute shipments. This could lead to information bottlenecks, making it difficult for all the different parties involved to get a clear picture of the situation.
But now, through the use of logistics technology, both shippers and carriers have the capability to not just react faster, but to predict and mitigate supply chain problems. Logistics technology can enable freight shipping companies to also fortify the overall resilience of the supply chain. This fortification is important in making sure customers receive certain goods on time, despite unexpected events and delays. This is especially true for areas of rural Australia.
The role of technology solutions for logistics
The main purpose of technology—regardless of industry—is to streamline complex processes and tasks. But what does this mean, exactly? Focusing specifically on the logistics and road freight industry, this comes down to a few key elements:
- Automation of routine tasks: Automation of routine tasks such as data entry, shipment scheduling, and invoicing leaves workers with more time to dedicate to other projects and tasks. This not only speeds up operations but also reduces human error.
- Tracking and visibility: Greater oversight and visibility allows shippers to monitor the location and condition of their cargo, which in turn enables them to provide detailed information to customers. This enhances security, reduces theft and loss, and improves service quality and customer satisfaction.
- Enhanced communication: Cloud-based technology can help to facilitate seamless communication and collaboration between all parties involved in the supply chain. This improves coordination, empowers informed decision-making, and enables a more agile response to changes or disruptions in the supply chain.
- Optimisation of routes and loads: Algorithms and software solutions enable carriers to optimise delivery routes and loads, reducing fuel consumption and increasing the number of deliveries per trip. This not only cuts operational costs but also minimises the environmental impact.
Overcoming logistics challenges through technology
When companies—both shippers and carriers—invest in technology to help them optimise their supply chains and logistics processes, everybody wins. The logistics industry has not traditionally relied heavily on technology. However, recent local and global events have meant that the companies that have already integrated technology into their logistics processes are the ones who are outstripping the competition.
Keeping goods moving through major disruptions
In March 2024 in Western Australia, heavy rainfall in the Northern Goldfields and Nullabor regions closed roads and railway lines. This left communities cut off from supplies, and time-critical freight (such as fresh produce and chocolate eggs ready to hit shelves for Easter) needed to be rerouted.
When the rain didn’t stop and the water began to rise to dangerous levels, all the usual goods were on their way for delivery, many of them heading to supermarket shelves. Speaking to ABC Radio in WA, Ofload’s Founder and CEO Geoffroy Henry explains, “All of [these goods] either got stuck on the trains that were on the rail, or stuck in the depots waiting to be moved. So this rain has created a lot of issues.”
When natural disasters and sudden, unforeseen events cause logistics disruptions like this on such a massive scale, it’s essential that shippers and carriers are able to pivot quickly to ensure deliveries aren’t left stranded and customer demand is met.
“When we saw the rising floodwaters [in WA], we contacted the entire Ofload network and started building contingency plans and booking shipments within hours,” says Geoffroy. By leveraging Ofload’s extensive, nationwide carrier network, Ofload was able to help the Australian Rail Track Corporation (ARTC) move high-priority frozen and refrigerated goods off the trains and on towards their final destinations.
Rapid responses to unexpected environmental disasters
“Everything is being unloaded [from the trains] progressively,” Geoffroy says. “[Ofload] has worked with every single supplier to move some other stock that they had and to make sure that we hit the road running… We’ve booked about 100 trucks in just a couple of days.”
It’s this kind of lightning-fast response that is so critical when facing unexpected disruptions to the supply chain. The threat here is that perishable goods will be ruined before they can even reach supermarket shelves, and that customers will need to go without essential items. But with the help of technology, companies in the logistics sector can adjust their strategies and work on alternative freight management solutions to ensure products reach their customers on time. This ensures the resilience of supply chain management even under the most extreme circumstances.
Building future-proof supply chains with technology
The reality is that with the growing volatility and complexity of the global market, shippers and carriers have to shift towards more proactive, technology-driven supply chain models. Prioritising preparation and preparedness by leveraging technology can allow companies to quickly adapt to major disruptions, and even foresee certain events. This proactive approach not only ensures efficiency despite severe challenges, but also sustainability and resilience.
Proactive supply chain management for improved resilience
The most important reason for building a proactive and resilient supply chain model is to ensure that freight arrives on time, and doesn’t hit a backlog or just remain idle. This can create massive problems for supply chains, resulting in increased costs, dissatisfied customers, and potential damage to a company's reputation.
“A couple of years of la nina forced us to make sure that we could build a resilient supply chain internally,” Geoffroy says. “Now, our technology allows us in seconds to reach out to thousands and thousands of trucking companies to make sure that we can secure the capacity to support suppliers, farmers and the big brands out there. This means we can keep moving freight across any region that might be affected by flooding or fire.”
A proactive supply chain model can empower carriers and shippers to swiftly adapt to changes in market conditions, regulatory environments, and customer expectations. This can minimise the impact of disruptions when they occur. Integrating this technology-driven approach better equips companies to deal with the challenges of today, and to also thrive in the future.
“The ARTC is doing an amazing job,” says Geoffroy. “Everyone has come together in trying to make it work. And I love to see that happening, when things like this test the strength of an industry… It's been a real challenge, and everyone involved has worked extremely hard to find solutions.”
Enhancing Supply Chain Resilience
The resilience of supply chains in today's fast-paced and unpredictable world hinges on the deployment of digital tools and software. Ofload’s end-to-end freight solutions can provide shippers and carriers with the data and insights they need to plan optimised routes, make more informed decisions, and proactively identify bottlenecks. Actively planning ahead allows companies to anticipate supply chain disruptions, from weather-related events to geopolitical tensions.
Sign up with Ofload today as a shipper or a carrier and discover how our technology can empower your business.